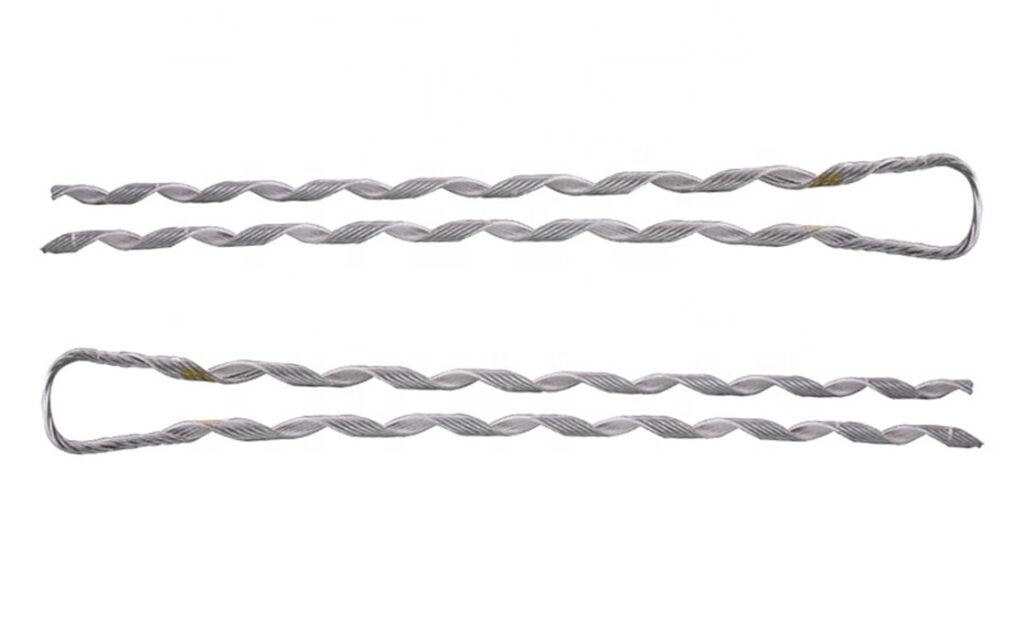
A preformed tension clamp is a hardware component designed to provide a secure and reliable means of supporting conductors under tension. It works in conjunction with overhead power lines to ensure proper tensioning and sag in the conductors. The main purpose is to maintain the integrity and functionality of overhead transmission lines. Its design id pre-formed to fit the specific diameter and shape of the conductor it is to support. This design helps to handle the tension forces in the conductor and maintain the grip. It is from materials with high strength such as aluminum ally or steel. This ensures the durability and resistance to environmental conditions. Their corrosion resistance design withstands the environmental challenges in South America. Common types include helical tension clamps, armor rod clamp, aluminum clad steel and composite clamp. They find use in applications such as transmission line, sag control, vibration damping and repairs.
Key features of preformed tension clamp
Preformed tension clamps offer various features that contribute to stability and reliability. The following are the features of the preformed tension clamps.
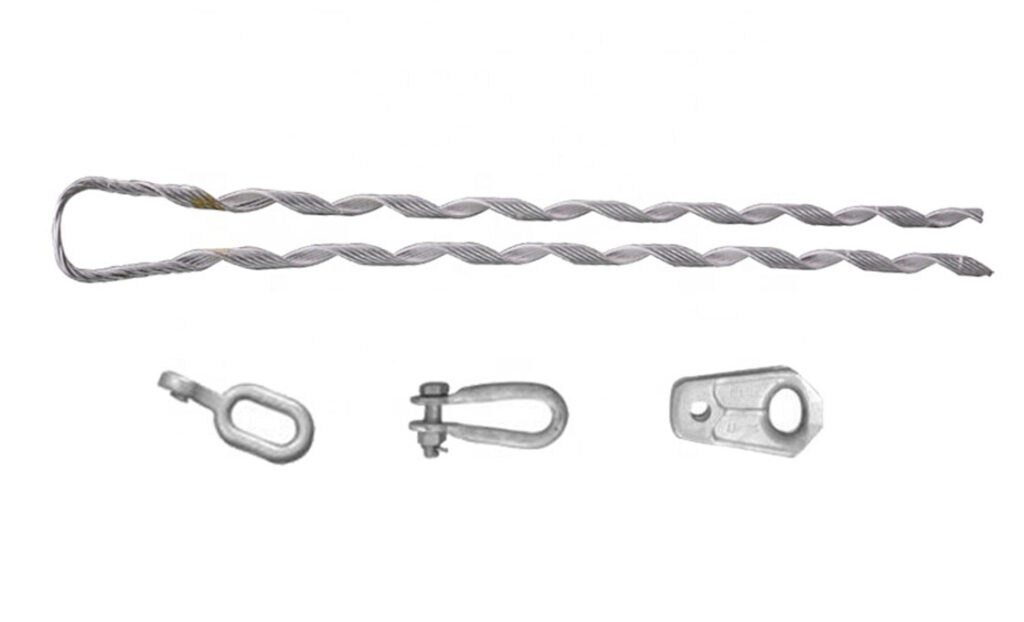
- Compatibility – the clamps have designs to work with other accessories and hardware used. This helps to simplify the integration of the clamps into the transmission design.
- High mechanical strength – the clamps provide high mechanical strength. They also help to ensure they can withstand the tension forces.
- Corrosion resistance – it helps to resist corrosion in environments with high humidity or salt exposure.
- Ease of installation – their design allows for quick and efficient deployment. This is during construction, maintenance and repairs.
- Preformed design – the clamps have various designs to match the specific diameter and configuration of the conductor.
- Material composition – the material should ensure the stability, strength and resistance to environmental conditions.
- Versatility – the clamps have designs that make them suitable for various transmission line projects.
- Tension change – the clamps are able to adjust to changes in tension within the conductor. This is during various weather conditions.
- Suspension capabilities – preformed tension clamps have designs for specific applications to anchor conductors.
Selection and installation of preformed tension clamp
Selection process is a crucial aspect of designing and constructing overhead transmission lines. The choice depends on various factors related to the specific requirements of the project. These include conductor type and size, application type, environmental conditions, load tension requirements and ease of installation. The installation process should ensure proper functioning and stability of overhead transmission lines. The following is a general guide on how to install preformed tension clamps.
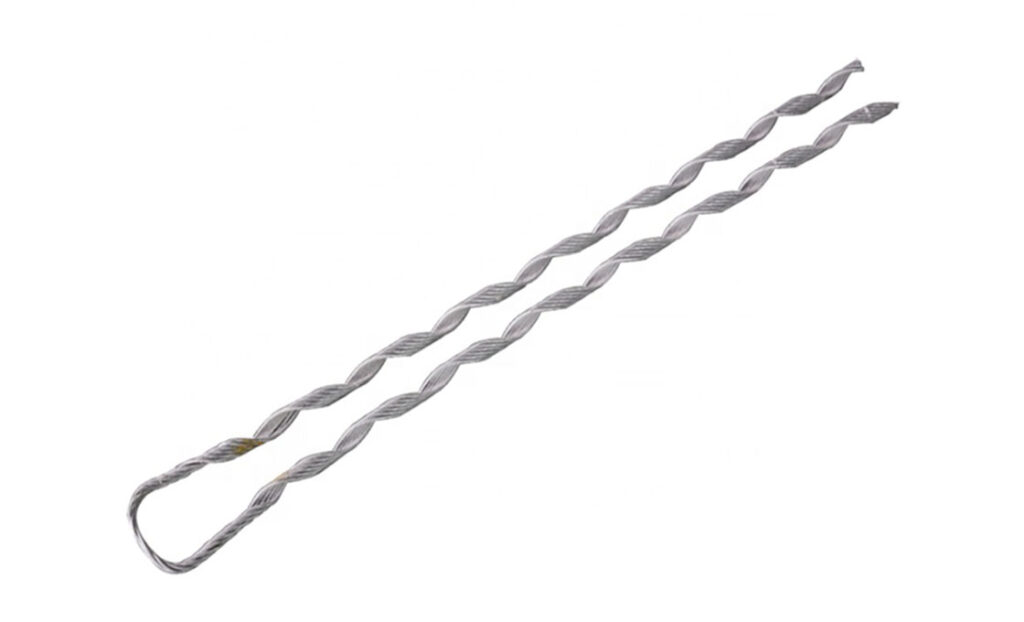
- Preparation – gather all the necessary tools required for the installation. This is including the clamps, wrenches and tensioning equipment. Use appropriate persona protective equipment and follow safety precautions.
- Clamp inspection – inspect each preformed tension clamp for any signs of damage or defects. Ensure the correct type of clamp for the conductor.
- Conductor preparation – prepare the conductor by cleaning it and removing any dirt or rust. This ensures a secure and reliable connection between the clamp and the conductor.
- Position the clamp – position the preformed tension clamp on the conductor at the desired location. Ensure proper alignment with the conductor’s diameter.
- Secure the clamp – use the suitable tools to tighten the nuts on the clamp following the manufacturers
- Change for sag control – adjust the clamp to achieve the desired sag in the conductor following the guidelines.
- Tensioning – use tensioning equipment to adjust the tension in the conductor if the transmission requires tension levels.
- Verify installation – check the clamp is securely attached to the conductor and all nuts and bolts are tight.
- Final inspection – conduct a final inspection checking for signs of stress, damage or misalignment.
- Documentation – maintain detailed records of the installation process. This is including any adjustments made and torque value.
Maintenance and inspection of preformed tension clamp
Regular maintenance and inspection of the clamp helps to ensure the continued reliability and safety. It also helps to identify and address potential issues that lead to failures and accidents. Additionally, the frequency depends on the diverse environmental conditions in the installation region. The following is a basic guide on maintenance and inspection of preformed tension clamps.
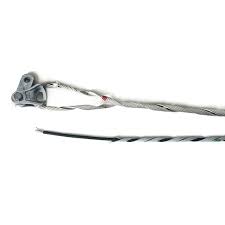
- Conduct routine visual inspections at regular intervals. This is either quarterly or semi-annually depending on environmental conditions. Check for signs of wear, corrosion or damage and deformation.
- Perform thorough inspections to identify any damage caused by high winds or other conditions.
- Perform a detailed inspection to ensure all components are properly installed and functioning as intended.
- Verify the preformed tension clamps are in good condition and that adjustments are correct.
- Clean the clamps to remove dirt, debris or contaminants especially in areas with high levels of pollution.
- Examine the clamps for signs of corrosion which may compromise their structural integrity.
- Check the tightness of nuts and bolts on the preformed tension clamp. Loose fasteners can result in reduced clamping force and compromise their performance.
- Inspect the clamp for proper functionality and ensure it is operating and there are no signs of wear or damage.
- Assess the shape of the clamp to ensure no distortotion. Provide proper support to the conductor.
- Inspect the preformed tension clamps for wear, deterioration or damage. replace any damaged inserts to maintain proper clamping.
- Check the alignment of the conductors to prevent uneven stress distribution and performance.
Comparative analysis of preformed tension clamps in South America
Conducting a comparative analysis involves considering various factors. These factors influence their selection, performance and suitability for the diverse conditions. Considering these factors helps in selecting preformed tension clamps suited for specific conditions. Additionally, it is advisable to consult with industry experts for guidance on the best preformed tension clamp in the market. The following are the factors to include in a comparative analysis in South America.
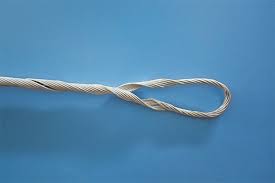
- Supplier network – consider the availability and reliability of suppliers of preformed tension clamps.
- Manufacturer reputation – consider the presence and support of preformed tension clamps manufacturers.
- Installation and maintenance – compare the ease of installation of different preformed tension clamps. Consider factors such as terrain accessibility and the availability of skilled labor. Examine the maintenance needs of various clamps considering the feasibility and cost effectiveness.
- Conductor types and sizes – analyse the versatility of the clamps to accommodate the various conductor types and sizes used in the transmission.
- Vibration damping – consider the effectiveness of the clamps in damping vibrations. They are mainly caused by winds in regions prone to high wind loads.
- Material – check the corrosion resistance of preformed tension clamps given the potential exposure to salty air in coastal area.
- Environmental conditions – consider the adaptability of preformed tension clamps to the unique environmental challenges.
Certifications and standards in South America
There are various certifications and standards for preformed tension clamps in South America. They ensure the quality, safety and performance of preformed tension clamps. Specific standards vary depending on country. Additionally, it is advisable to ensure the selected preformed tension clamps complies to all the relevant industry standards. The following are the common certifications and standards in South America.
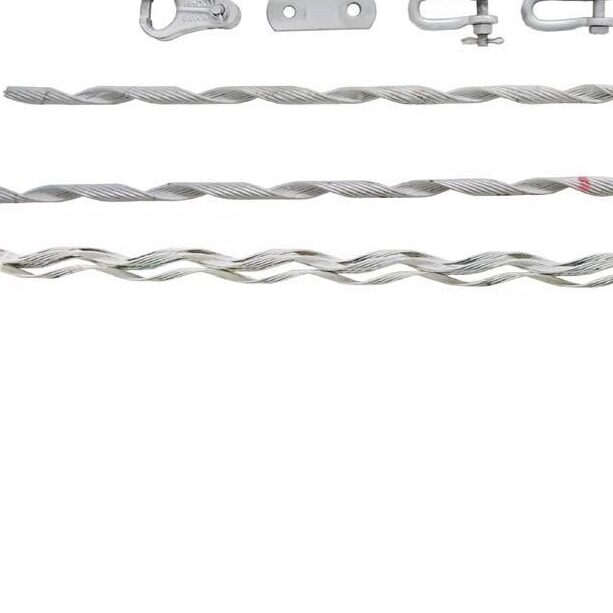
- ISO certification – this demonstrates the manufacturers quality management system to ensure consistent product quality.
- IEC standards – this specifies requirements and tests for fittings for preformed tension clamps.
- ANSI standards – these are standards related to components including preformed tension clamps.
- ASTM standards – these are international standards for materials and products such as coatings and steel hardware.
- Local electrical standards – each South American country has its own set of electrical standards. This may include specifications for design, materials and testing of components used.
Regional market for preformed tension clamps in South America
There are various factors that shape the market for preformed tension clamps in South America. It is dependent on various factors such as expansion of electrical infrastructure, technological advancements and environmental conditions. Additionally, it is advisable to consult industry professionals for guidance on market trends and dynamics. The following are the factors that influence the regional market in South America.
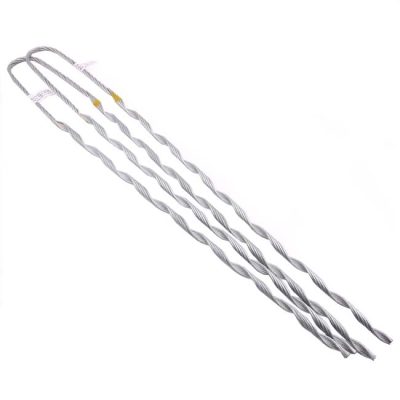
- Renewable energy projects – the increasing emphasis on renewable energy sources such as wind and solar contributes to the need for transmission lines.
- Environmental considerations – the diverse environmental conditions that necessitate preformed tension clamps.
- Economic factors – economic stability and investment climates influence the implementation of energy projects.
- Technological advancements – innovation leads to the development of more efficient and durable preformed tension clamps.
- Project financing – the availability of financing for energy projects affects feasibility and execution of transmission line projects.
- Local manufacturers – the availability of local manufacturers and international imports may influence the market dynamics.
Frequently asked questions
A preformed tension clamp is a device used to provide mechanical support and maintain the tension of conductors. They are pre-shaped to match the conductor’s diameter allowing for easier installation and optimal performance.
Preformed tension clamps help to accommodate various conductor types and sizes commonly used in South American transmission projects. They can work with aluminum, steel or composite conductors.
The clamps contribute to the reliability of overhead transmission lines by securely supporting conductors, minimizing sag and reducing the risk of conductor detachment.