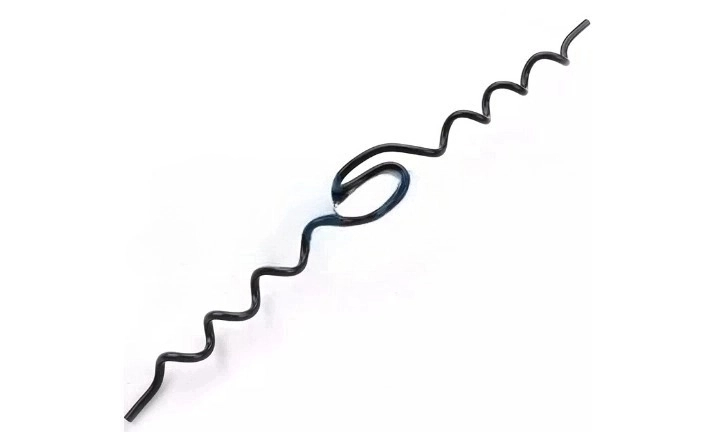
A top tie refers to a specific type of fastening or securing mechanism to attach the conductor to the insulator. Its design ensures minimal electrical resistance and mechanical stability. This is for safe operation of the transmission line. The top ties main function is to hold the conductor in place and ensure it remains attached to the insulator. It also ensures the conductor positions at a safe distance from the pole to prevent electrical arcing. Top ties reduces the movement and friction that can cause wear over time. Top ties are from durable, corrosion resistant and high strength materials. These materials include galvanized steel, aluminum or composite materials. They serve functions in various applications in the electrical transmission industry.
Accessories used with a top tie in overhead transmission lines
There are several accessories that work with a top tie to ensure the stability, safety and efficiency of the transmission system. Each of these accessories serve a specific purpose in overhead transmission lines. The conjunction helps to reduce maintenance needs and prolong the systems lifespan. The following are the common accessories used with a top tie in overhead transmission lines.
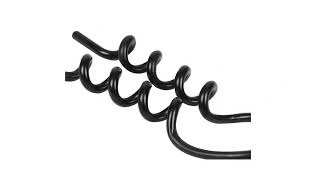
- Insulators – these components support and electrically isolate the conductors from the poles. Common types of insulators include pin-type, suspension and post insulators.
- Spacers – these help to maintain the proper spacing between conductors in a multi-conductor bundle. This prevents the conductors from clashing and ensures consistent electrical performance.
- Armor rods – these wrap around the conductor at the point of attachment to protect it from abrasion and mechanical stress.
- Vibration dampers – these are devices installed to reduce the amplitude of conductor vibrations.
- Preformed ties – these have designs to fit specific conductor sizes and insulator types. This is to provide a secure and uniform attachment.
- Line guards – these offer protection against mechanical damage and electrical stress. This is especially in areas with high pollution.
- Bird guards – these serve to prevent birds from perching on insulators and causing contamination.
- Arcing horns – these are protective devices used to divert electrical arcs away from insulators during lightning strikes.
- Corona rings – these help to distribute the electric field around the insulator and reduce corona discharge.
- Clamps and brackets – these help to secure the insulators and other accessories to the tower structure.
Coatings and treatments for a top tie
Top ties face various environmental conditions and mechanical stresses. Coatings and treatments enhance their durability, corrosion resistance and performance. Selection of these coatings and treatments depend on the specific environmental conditions and mechanical requirements of the transmission line. The following are the common coatings and treatments for top ties.
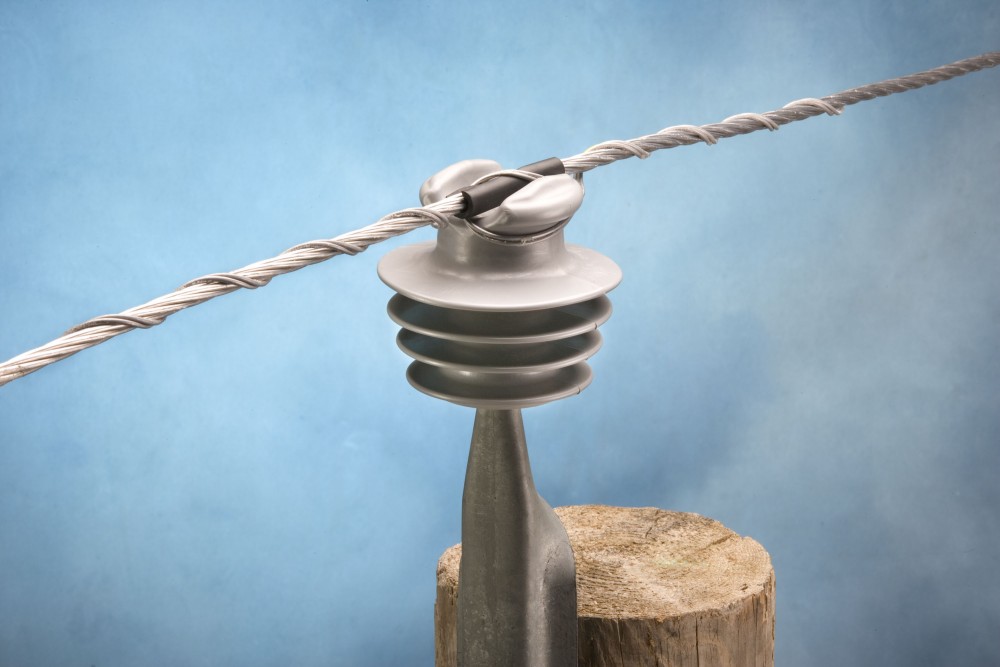
- Galvanization – this includes hot-dip galvanizing where the tie inserts into molten zinc. This proccess is to form a corrosion-resistant coating. It also includes applying a zinc coating through an electrochemical process to provide a smooth finish.
- Aluminum coating – this includes spraying molten aluminum onto the top tie’s surface to create a protective layer. This layer provides excellent corrosion resistance ideal for coastal or polluted areas.
- Polymer coatings – epoxy coatings provide a tough, chemical-resistant barrier that protects the top tie from corrosion and mechanical damage. Polyester coatings apply as powder and then cured to form a durable and UV resistant coating.
- Phosphate treatment – this is a chemical treatment that involves applying a phosphate coating. The coating enhances the adhesion of coatings. It also provides a degree of corrosion resistance.
- Anodizing – this is an electrochemical process that increases the natural oxide layer on aluminum top ties. This provides enhanced corrosion resistance and surface hardness.
- Painting – this is applying specialized paints to top ties to provide a layer of protection against corrosion and UV degradation.
- Passivation – this is a process that enhances stainless steel top ties by removing surface contaminants. The process also promotes the formation of a protective oxide layer.
- Zinc-aluminum coatings – these are coatings applied through thermal spraying or dipping. It combines the benefits of zinc and aluminum. They provide superior corrosion resistance for use in harsh environments.
Technical specifications for a top tie
Technical specifications for a top tie provide guidelines and details for their use and standards. They vary depending on the application, conductor type, insulator design and environmental conditions. The technical specifications ensure the top tie performs well to provide mechanical support, electrical conductivity and environmental durability for overhead transmission lines. The following are the technical details for top ties.
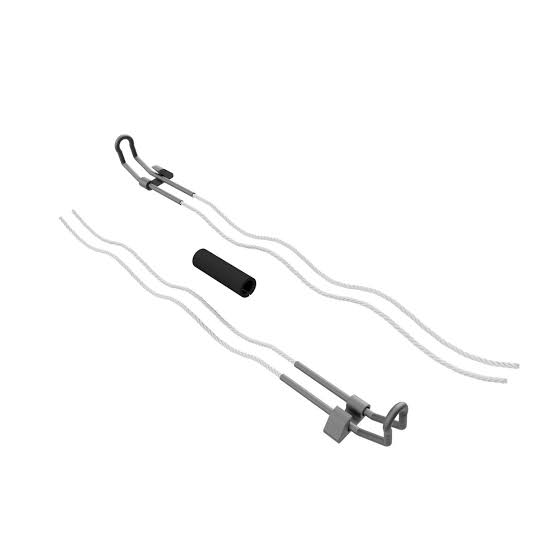
- Material composition – top ties are from various materials including aluminum alloy, galvanized steel and copper. Each of these materials provide several benefits such as high strength, corrosion resistance and durability.
- Mechanical properties – top ties should have tensile strength and provide flexibility. This is to be able to withstand forces exerted by the conductor and environmental conditions.
- Dimensions and size – the length of the top ties varies depending on the insulator and conductor size. The diameter should match the conductor size to ensure secure fit and handle mechanical and electrical load.
- Coating and surface treatment – these include galvanization, aluminum coating and polymer coatings. They include specifications for the thickness of the zinc coating, thermal spraying and type of epoxy of polyester coatings.
- Electrical properties – this includes details for current carrying capacity and electrical resistance. The current capacity should match or exceed the conductor’s current carrying capacity. The top tie should have low electrical resistance to reduce power losses.
- Environmental resistance – the top tie should be able to withstand factors that lead to corrosion. They should also be UV resistant to ensure longevity under sunlight exposure.
- Compatibility – the specifications should provide details for conductor compatibility and insulator compatibility.
Industry advancements and updates for top ties
There are recent advancements in the industry for top ties that focus on improving their durability and efficiency. The industry aims to enhance the performance and reliability of the top ties for efficient use in overhead transmission lines. Additionally, it is important to stay updated to ensure the best performance of the applications. The following are the key advancements and updates for top ties.
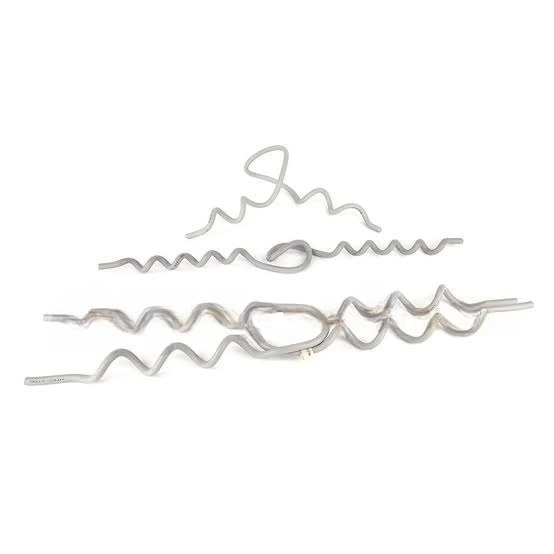
- Advanced materials – development of high strength composite materials provides durability and corrosion resistance. Use of Nanocoatings enhances surface properties to provide superior resistance to corrosion and wear.
- Improved coatings and treatments – this is the development of hybrid coatings that combine different coating materials. This is to enhance performance characteristics like higher corrosion resistance and longevity. There are also innovations in coatings that can repair minor damages automatically. This helps to maintain their protective properties.
- Enhanced design and engineering – this is designing top ties with aerodynamic shapes. Such shapes reduce wind-induced vibrations. Preformed top ties provide a more secure fit since there are specific to conductor sizes.
- Smart monitoring and diagnostics – this includes embedding sensors in top ties to track stress, temperature and electrical load in real time. Leveraging the IoT to collect and analyse data from many top ties eases management and fault detection.
- Cost effective solutions – use of advanced manufacturing techniques reduces costs and improves the precision of top tie components. Designing modular top tie systems that can be easily replaced reduces labor costs and downtime.
- Environmental adaptations – there is development of environmentally friendly coatings that reduce the ecological footprint of manufacturing processes.
Troubleshooting top ties in overhead transmission lines.
Troubleshooting a top tie involves several processes of identification and addressing various issues. Maintenance also helps to maintain the top ties and ensure their reliability in overhead lines. Additionally, it is advisable to conduct professional maintenance and inspection once in a while. The following is a basic guide to troubleshooting a top tie.
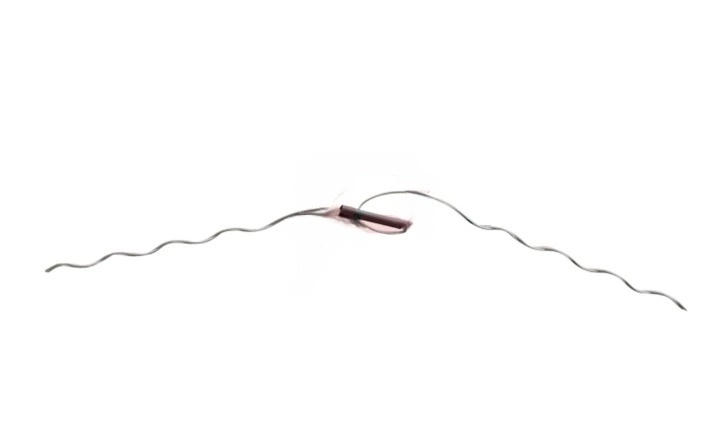
- Visual inspection – check for signs of rust, oxidation or other forms of corrosion on the top tie and its coatings. Check for physical damage and loose connections.
- Mechanical testing – use a tensile tester to check the mechanical strength of the top tie. Compare the results with manufacturers specifications. Bend the top tie to see if it maintains its integrity without breaking.
- Electrical testing – measure the electrical resistance across the top tie to ensure its within acceptable limits.
- Environmental analysis – check for UV damage and signs of pollution-related damage. This is including deposits from industrial environments.
- Advanced diagnostics – use thermal imaging to detect hotspots that can state poor electrical connections. Conduct vibration analysis to identify issues that could lead to mechanical fatigue.
- Sensor data review – review data from embedded sensors to check for unusual stress or load patterns. Check for temperature anomalies the might show electrical or mechanical issues.
- Remedial actions – this includes cleaning, tightening, replacing damaged components and re-coating.
- Documentation – document all findings, test conducted, and actions taken. Provide recommendations for ongoing maintenance.
Frequently asked questions
A top tie is a fastening mechanism used to secure the conductor to the insulator on the top of utility pole.
Common accessories include insulators, spacers, armor rods, vibration dampers, preformed ties, line guards, corona rings and clamps and brackets.
Common coatings and treatments include galvanization, aluminum coating, polymer coatings, phosphate treatment, anodizing and zinc-aluminum coatings.