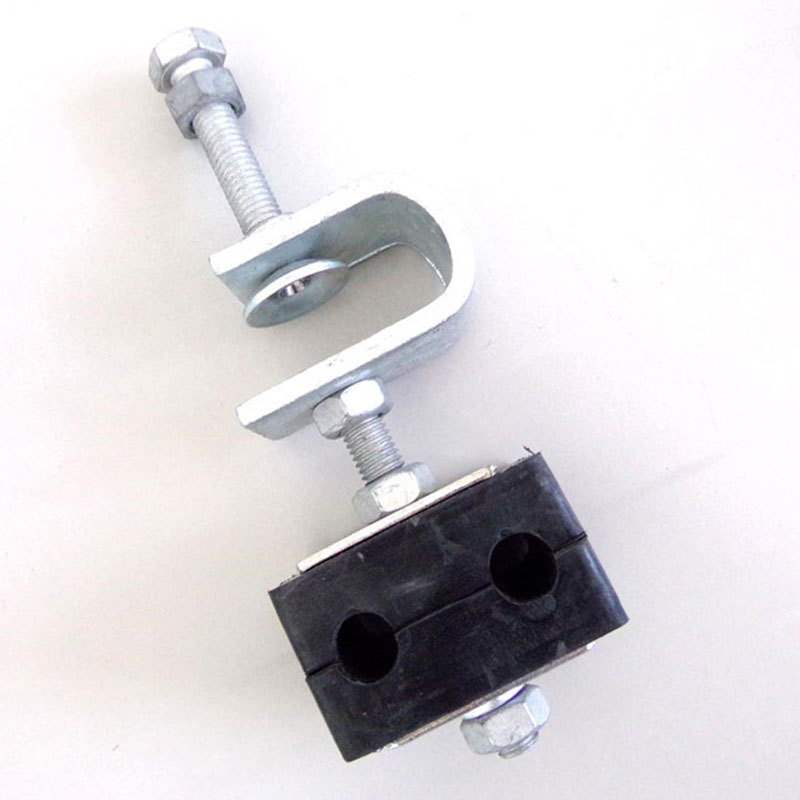
A downlead clamp is a specialized component used to guide and secure fiber optic cables as they leave the transmission line. It is sometimes referred to as wire clamps, cable clamps or downlead cushions. The fiber optic cables depend on downlead clamps for support and shield. It shields the fragile fibers from excessive movement, vibration and abrasion. On the transmission lines, the clamps guarantee correct cable alignment and routing. By doing this, you can preserve signal quality and lessen the strain on the wire. Fastened, suspension and compression downlead clamps are examples of common types. The kind and diameter of the cable, the location and the surrounding circumstances all influence the clamp selection. A downlead clamp can find use in a variety of electrical industrial applications. This covers initiatives involving building, renewable energy, power and telecommunication lines.
Materials used in making a downlead clamp
Downlead clamps have particular features to endure harsh environments and offer dependable cable support. A variety of materials are necessary in the production of downlead clamps. Additional considerations for the chosen materials include the application, climate and particular needs. It’s also a good idea to speak with professionals in the field to get advice on the best content for your application. The following are typical downlead clamp materials.
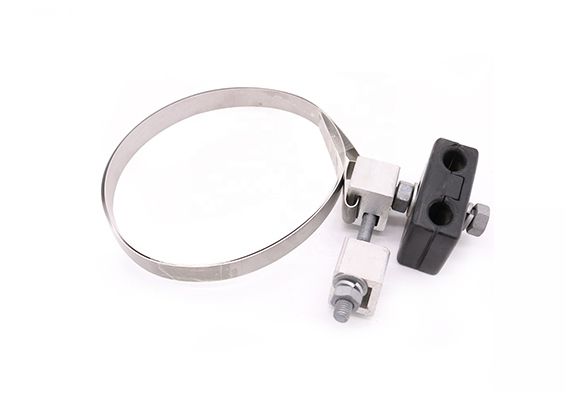
- Aluminum – this is a lightweight metal that resists corrosion well. It is therefore appropriate for outdoor use.
- Composite materials – materials classified as composites include fiberglass-reinforced plastics. They provide resilience to corrosion, strength and durability. They are frequently seen in fiber optic cable clamps.
- Galvanized steel – this offers strength, durability and corrosion resistance. Zinc coats the steel as part of the galvanization process to prevent rust and corrosion. It is hence appropriate for outdoor applications and harsh environmental conditions.
- Copper – this is a highly effective electrical conductor that finds use in situations where conductivity is necessary. Coatings may work on copper clamps to increase their resistance to environmental elements.
- Stainless steel – this is a material that offers exceptional durability and strength. Applications like coastal or marine areas can use it. The most common places to find it are in clamps such as tower, wrap-around and U-shaped clamps.
Characteristics of downlead clamps
Downlead clamps offer a number of characteristics that help to support and secure cables. The qualities change based on things like the type of material used, the requirements for the design and the intended usage. These qualities contribute to long-term dependability and security. The common characteristics of the downlead clamps that are now on the market are as listed below.
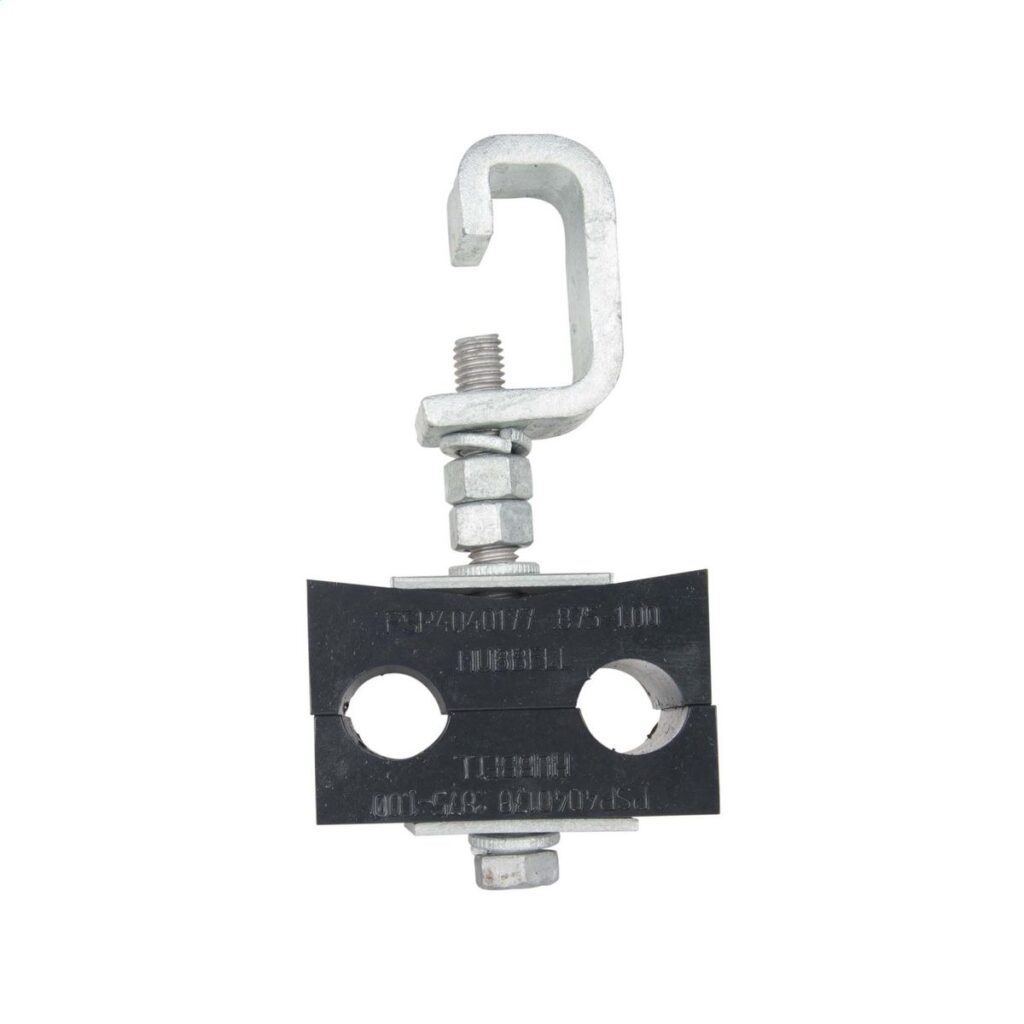
- Durability – the clamps ought to be strong and resistant to rust, corrosion and deterioration with time. This keeps them functional even under different conditions.
- Corrosion resistance – the clamp has protection from rust and corrosion by materials like aluminum, stainless steel and galvanized steel. This is due to the fact that they install in conditions that include mechanical wear, moisture, UV rays and temperature swings.
- Weather resistance – this is important since downlead clamps need to be able to survive a range of weather conditions. This covers severe weather conditions like wind, rain and snow. This is without sacrificing their structural integrity or usefulness.
- Ease of installation – installing them should be simple and they should work with a variety of cable sizes and types thanks to their features.
- Strength – the clamps need to be strong enough to hold the weight of the wires or cables. This guarantees that the cables won’t droop or slip in their current location.
- Electrical insulation – to avoid contact between conducting materials, downlead clamps have electrical insulation. They also aid in lowering the possibility of short circuits or other electrical risks.
Certifications and testing for downlead clamps
By following these procedures, you can make sure that the necessary electrical parts fulfill industry requirements for quality, performance and safety. The testing options vary based on the locale and the clamp’s intended use. Certifications from reputable standards organizations or regulatory agencies are available via the tests. The effectiveness and quality of electrical installations enhances by the downlead clamp certifications. Consult industry experts for advice on suggested certifications. The several tests and certifications for downlead clamps are as shown below.
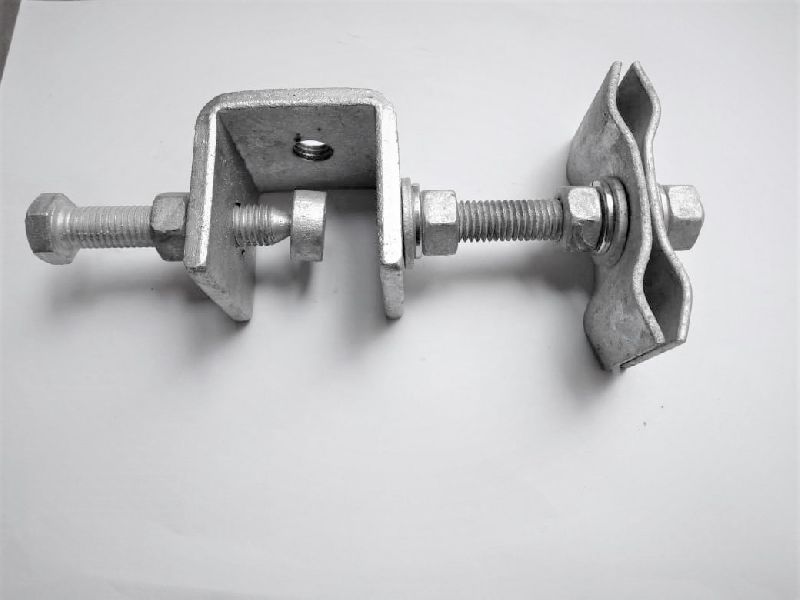
- Mechanical testing – this evaluates the downlead clamps’ mechanical qualities and structural soundness. This includes their resistance to deformation, load capabilities and ability to tolerate mechanical stress.
- Electrical testing – to confirm the electrical insulating qualities of some clamps, electrical testing is essential. Additionally, they guarantee that they offer enough defense against electrical risks.
- Material testing – these examinations check the characteristics of the materials utilized in their manufacture. They consist of durability, corrosion resistance and tensile strength. This guarantees that the materials fulfill the required performance and reliability standards.
- Certifications – it can be necessary for the clamps to get certifications from reputable standards groups. This demonstrates adherence to rules and industry norms. There are several certifications for the clamps, including IEC, CE and UL certifications.
- Environmental testing – this type of testing evaluates how well downlead clamps function in various environmental settings. This covers exposure to chemicals, dampness UV rays, and extremes in temperature.
- Internal testing and quality control – these procedures are from the majority of manufacturers. This is to guarantee that the downlead clamps fulfill their required specifications.
Drawbacks of downlead clamp materials
As previously stated, some factors influence the selection of the appropriate material for downlead clamps. These consist of desirable qualities, financial limitations, environmental factors and application needs. It’s also essential to seek advice from knowledgeable experts on the appropriate materials for your application requirements. The typical benefits and drawbacks of the materials used to make downlead clamps are as listed below.
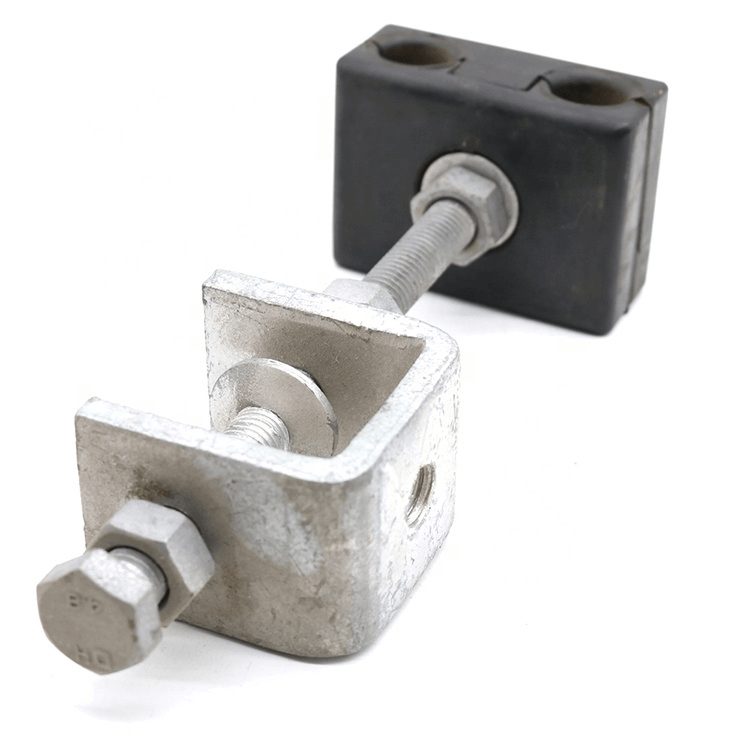
- When compared to other materials, galvanized steel may weigh more. Handling and installation may face drawbacks by this. In severe settings, it might potentially erode with time.
- When compared to other materials, stainless steel is more costly. Additionally, they might exhibit magnetic qualities, which might be important in particular situations.
- Because aluminum is not as robust as steel, its application in heavy-duty applications may be more limited. They may experience galvanic corrosion and are more costly than galvanized steel.
- Plastic materials offer electrical insulation, are rust and corrosion resistant, and are easy to work with. They might not be as strong as metal clamps, though, and they might break down in hot weather.
Technical details on downlead clamps
Depending on some variables, downlead clamp technical parameters change. These consist of the manufacturer’s design, industry standards and particular application. Please refer to the manufacturer’s documentation for precise information about the downlead clamp. This is to guarantee downlead clamp functionality and safety in electrical installations. The technical specifications for downlead clamps are mostly influenced by the following elements.
Model | Product Name | Cable Diameter | Weight(KG) | Remark |
TGY11.10 | Downlead clamp for pole | 9.0-11.1 | 0.9 | For ADSS and OPGW cable |
TGY13.30 | Downlead clamp for pole | 11.2-13.3 | 1 | For ADSS and OPGW cable |
TGY15.50 | Downlead clamp for pole | 13.4-15.5 | 1 | For ADSS and OPGW cable |
TGY18.00 | Downlead clamp for pole | 15.6-18.0 | 1 | For ADSS and OPGW cable |
TGY11.10 | Downlead clamp for tower | 9.0-11.1 | 0.95 | For ADSS and OPGW cable |
TGY13.30 | Downlead clamp for tower | 11.2-13.3 | 0.95 | For ADSS and OPGW cable |
TGY15.50 | Downlead clamp for tower | 13.4-15.5 | 0.95 | For ADSS and OPGW cable |
TGY18.00 | Downlead clamp for tower | 15.6-18.0 | 0.95 | For ADSS and OPGW cable |
- Electrical properties – these comprise details on compatibility, conductivity and electrical insulation.
- Size and capacity – this refers to the clamp’s length, width and diameter measurements. It also has the ability to hold cables or wires of particular kinds and sizes.
- Material – this refers to the variety of materials utilized in the production of the clamps. This covers aluminum, stainless steel and galvanized steel.
- Load rating – the greatest load that the downlead clamp can withstand without failing depends on its load rating. This is mainly measured in kilos or pounds.
- Temperature range – the range of temperatures that the clamp can function in without experiencing any degradation.
- Details about the manufacturer – a few include technical details on the downlead clamps. Name, model, batch code and part number are a few examples of information.
Frequently asked questions
The common materials used in the production of the clamps include galvanized steel, stainless steel, aluminum and plastic. Each of these materials provide different benefits and properties depending on the specific application.
Downlead clamps are commonly used in outdoor applications where they face exposure to environmental factors. It is advisable to select clamps that are from materials that are suitable for outdoor and provide corrosion resistance.
Installation requirements for downlead clamps vary depending on the manufacturer and specific application. It may need proper placement, alignment and securing od the clamp to a suitable support structure. This is essential to ensure effective cable management and long-term performance.